Enter a name, company, place or keywords to search across this item. Then click "Search" (or hit Enter).
Collection: Books and Periodicals > Mining & Scientific Press
Volume 28 (1874) (430 pages)
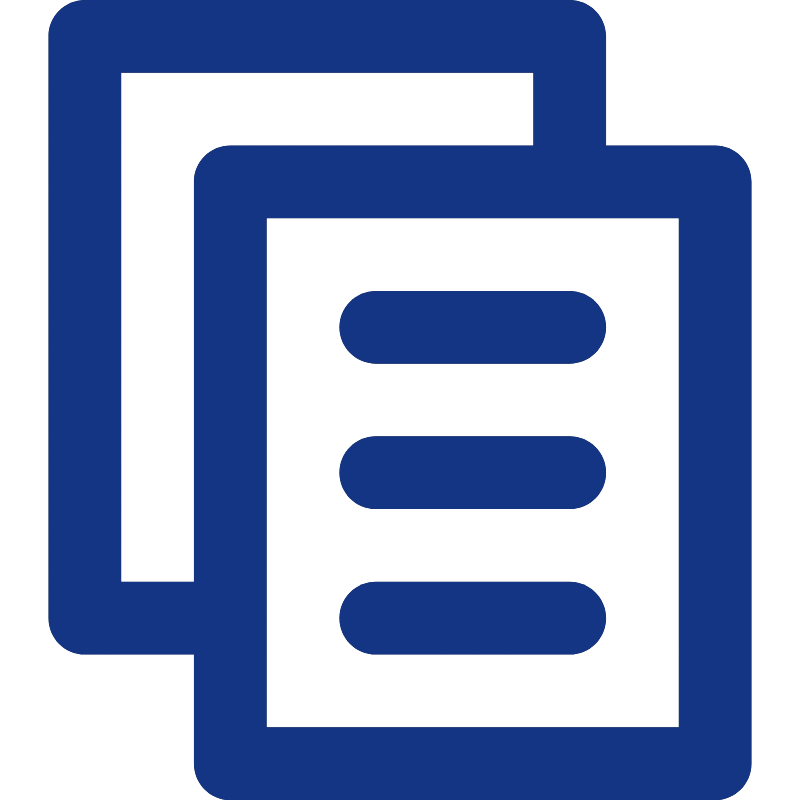
Copy the Page Text to the Clipboard
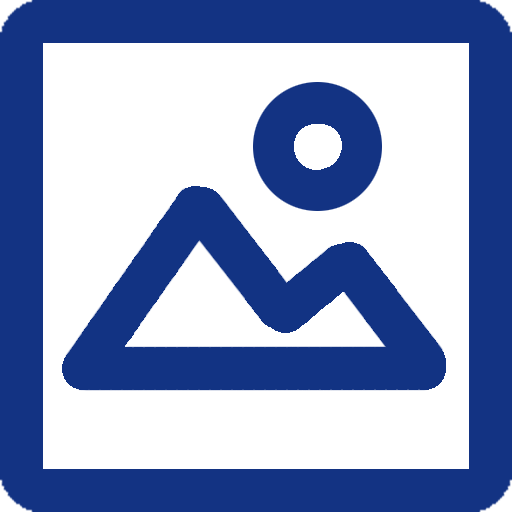
Show the Page Image
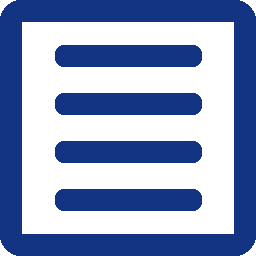
Show the Image Page Text
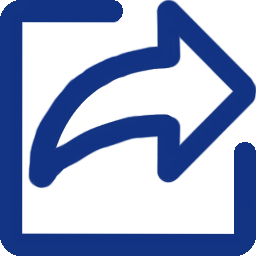
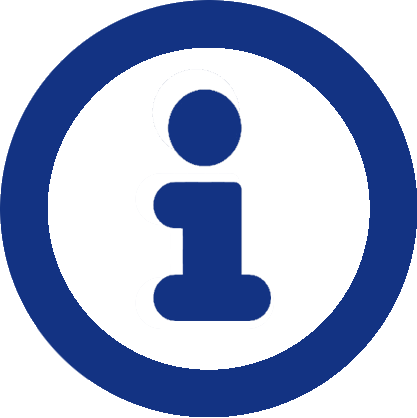
More Information About this Image
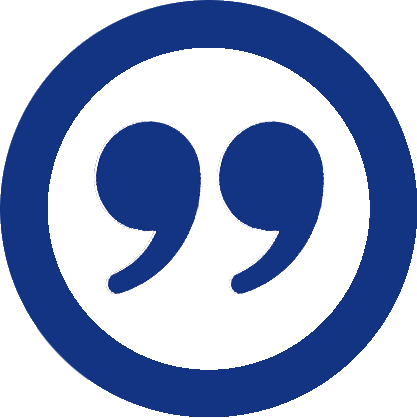
Get a Citation for Page or Image - Copy to the Clipboard
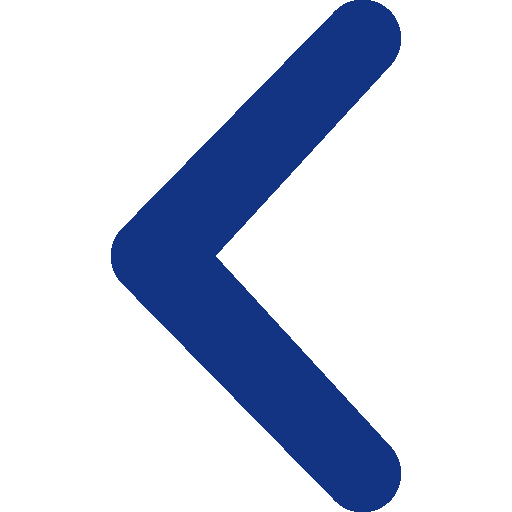
Go to the Previous Page (or Left Arrow key)
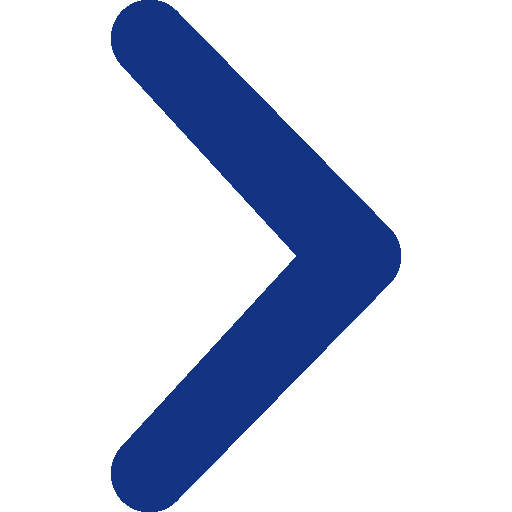
Go to the Next Page (or Right Arrow key)
Page: of 430
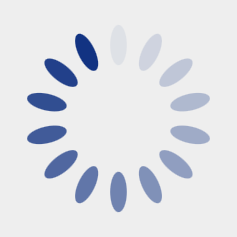
An Illustrated Jou rnal of Mining, Popular Science and Progressive Industry.
BY DEWEY & CoO.,
Patent Solicitors. SAN FRANCISCO, SATURDAY, JANUARY 10, 1874,
VOLUME XXVIII
‘Number 2.
Antimony Reduction—No. 2.
Tn onr last Issue wo made somo remarks on
tbe treatment of antimony and we now proceed
to consider the extraction of metallic antimony
direct from ores and also from the crude antimony. At present the greatest proportion of
antimony is still obtained from ernde antimony.
For this operation there are two principal
methods In ase; that is, it is effected either by
preeipitation with iron while smelting, or hy a
combined oxidation and reduetion process.
The treatment with iron gives good results, but
the antimony takea np some iron and requires
subsequent refining. Besides the iron,
sulphate of sodinm (Glanber salt), is taken
as a finx and some pniverized charcoal
also added, Autimony and sulphide of
iron are formed, which nnite with the
resniting snlphide of sodium. This, salt
forms aliqnid cover over the metal and
preventa its volatilization to a great extent. Soda in place of Glanher salt gives
a less liqnid finx and is, besides, more
expensive, ae
‘The furnace nsedis similar to tbat shown
in Fignres 1 and 2 of our engravings. The ™
concave bottom or crucible is beaten hard
and made of @ mixture of sand and clay,
being provided with a tap hole. In this
100 parts of crude antimony are mixed
with 42 parts of iron filings, and 10 parts
of enlcined Glanber salt, with an additiod of 3 parts of pulverized charcoal, or ~
with 50 parts of soda and 10 ‘of charcoal.
In eight or ten honrs about 330 ponnds of
the antimony is melted in. . © rad .
The smelting of ore for metallio antimony direct, snffers less loss than for crude
antimony. Poorer ores, from 30 to 40 ~~
per oent., are smelted in sbaft furnaces
with threé tnyeres. ‘The furnace is 11
feet high from the tnyeres, 3 feet deep and
2%, feet wide.’ The ore is pulverized and
roasted in a reverberatory fnrnace, oné
ton in six hours, and smelted with coke in
the above shaft furnace. With poor ore.
the smeltiigin a shaft furnace is more
sconomical than in a crucible’ furnace. ,
For the pnrpose of smelting the ore in a}
reverberatory furnace, if no iron is nsed
for precipitation, a csrefn] roasting is
required. ‘This is’ best performed in a
reverberatory roasting fnrnace, like that ;
shown in Fig. 3, and the pulverized ore is in-.
trodnced throngh the arch and stirred at a low:
heat until all the sulphur is driven out. The
loss in roasting is, of course, very variable,
but,Zwith a careful roasting and proper ore,
only from 1% to 2 per cent. volatilizes. The
roasted ore is then mixed with uuroasted, oxidized ore, if such is obtained from tho mine,
and the whole mixed with from 22 to 30 per
cent. flux (salt, Glauber sslt and soda), and
15 or 20 per'cent. of powdered charcoal, besides some slag from the former charge. The
roasting furnace, as well as the smelting furnao, ia provided with dust-chambers, where a
part of the volatile antimony is deposited,
whichis alao added to the ore mixture, . : '
The furnace shown in Figs, 1 and 2represents
the smelting furnace. The crucible is lined
with, firé' olay’ and when red hot the ore is
oharged up to 650 pounds, the door is closed
for a'short time and the fire Immediately started. Much stirring is required for four or five
honrs and the scum.is ocoasionally drawn out.
After six hours the smelted mass is tapped and
metal and slag run into a small hearth in front
i
o{ the furnace, When cold, the regulus is
taken out, the slag separated and the antimony
metul hrokeu into pieces for further refining.
The loss of antimony by this process is about
15 percent. The refining process is mostly
earried on in crucibles with a proper finx,
which is the same us used for the smeltirg of
ore, consisting of sulphate and carbenate of
soda and sslt. If there isarsenic iu the metal,
it is well to introduce from time to time a piece
of saltpeter into the erncible and stir the msss
with a clay stirrer. Mr. A, F. Wendt, in
Csnads, nses a large reverberatory furnace, 40
.drawn every 24 honrs, so that the ore, remains
feet long and 9 feet wide. According to the
WEED
Vy
EES Tipe?
Bee
Ng.2 i
reduced metal and fluxes the gaugue. In about
four honrs tho furnace is at a bright red
heat approaching whiteness, the whole mass is
in fusion and active ebullitien, and the carbonie
seid penrtrates the layer of slag as a bine
flame. The charge is now repeatedly stirred
until quite fused. The fire is then let dewn
and the doors opened until the slag becomes
thick and pasty, wherenpen it is drswn out.
As goon as it is removed, 25 pounds of saltcake and 10 pounds of charcos] are thrown on
the mets], snd the fire again raised. In one
honr and a half the slng is iu a state of fnsion
as iqnid as water. The metal is ladled into
Late
~«
3
a ; FURNACES FOR REDUCING ANTIMONY.
Engineering and Mining Journal, which describes
Mr. Wendt’s furnace, it has ten working doors
aud holds five charges, three of 600 pounds of
wet ore (concentrated) being introduced and
40 hours in the furnace. Every five or ten
minutes the ore hss to be stirred to prevent
agglomeration. The loss by roasting is 734
per cent. Consumption of fuel, three-qnsrters
of a cord of wood in 24 hours.
Mr. Wendt combines smelting and refining
in ‘one operation, which is a great improvement in reducing antimony ores. The crucible
furnace is five feetin diameter and 18 inches
deep. The flux nsed in smelting is a crude sulphate of sodain the form of salt-cakes anda
charge usually consists of 500 pounds of roasted ore, 100 pounds of salt-cake and 75 pounds
of hardwood chargoal, all iu coarse powder.
About one half of a cord of wood is burned at
each charge. The ore is mixed with the chareoal and spread evenly in the retort furnace
‘being covered with a mixture of salt-cake and
charcoal. The fire is immediately increased
and a fused layer is formed which protects the
1
dishes holding 25 pounds each, care being
taken to dip enough slag, to cover the metal;
when cold the slag is broken off and the metal
is ‘perfectly fine.
Savina Monzy.—The report of O. C. Hewitt,
Superintendent of the Keystone Consolidated
mine, in ‘Amador county, is to the effect that
they have saved abont $5,000 per month by the
abandonment of blankets and buddles and the
use of Hendy’s concentrators. The concentrators have been in nse there ahont five months
and of conrse give great satisfaction, as they
have performed their work so well.
Tus Onovirne Mines.—The ‘Lava Bed”’
mines, near Oroville, continue to pan out to
the Chinamen, by whom they are worked. The
Chinese town near by is growing rapidly, and
numbers of celestials are swarming thither.
Tue Gould and Curry, Hale and Norcross,
and Imperial mines, are all down to the Sutro
tunnel level, and exploring at that point. The
Yellow Jacket is considerably below it, and the
A Startling Discovery.
Throngh the kindness of a gentleman of scientific tastes, residing iu this city, we were permitted to see recent nnmbersof the Afonilor Belge,
which contain references to the reported discovery, by a Belgian peasant, of a fact which,
if more substsntially verified, is destined to
eanse a complete revolution in the preparstion
snd use of fuel, and furnish a partial selution,
at least, of the difficult problem which hss so
long coufrouted British economists. The
statement is that it has been found that a mixCrown Point has penetrated 200 feet below it.
ture of coal slack, or waste screeuings aud dust,
with clay, mnd or other argillaceons matter, and sal-soda, may be made, which will
cost one-half as much, and burn beller,
than ordinary’coal. The ingredients are
thoroughly incorporated, aud taken in the
following proportions: coal slack, twentyfive parts; earthy matter, seventy-five
parts, and sal-soda, one per cent. The
whole virtue of the preparation rests, it is
said, on the action of the sal-soda. How
this substauce is capable of so assisting
comhnation as to oonsumesuch a dead
weight of wholly inert matter, is another
thing, and will puzzle onr chemists to explain, A mixture, among the thousands
constautly heing patented, especially in
England, consista of seventy-five part’
of coal dust, and twenty-five ’ parts of
clay. This manages to burn itself, yomewhatin the manner of peat, bnt is not
so valusble as a heat-producer as the
common coal, and is of qnestionable economy, inasmnch as the coal dnst alone, or
mixed with only enongh water having
elay in suspension to render the whole
consistent, in the form of bricks, is
much more effective, The trouble of
weighing and incorporating so small a
percentage is hardly compensated for by
the trifling saving in material. But in the
neW composition, ouly one-fourth of the
entire mass is coal. It would even pay
to expressly crush block coal on this
system, if all that is claimed be true.
The discoverer, or inventor, has not patented his improvement, and its benefits are free tothe world. It is further
stated that manufacturers and other
large fnel nsers in Belgium are making
. trialof the compound with satisfactory
results. Weawait further and more detailed
information before commenting at length upon
this last sensation.
‘Rich Ore. :
We have jnst been shown a sample of about
seventy ponnds of exceedingly rich ore oontaining free goldin abundance, taken from the
Patterson mine at Tuttletown, in Tnolumne
county. This mine belongs to Mr. J. J. Corrigan, (now on his way to London, England).
He is the principal resident director here in
San Francisco of the celehrated Richmond
mino, at Enreka, Nevada.
Mr. Corrigan deserves to he congratulated on
bis success in developing the Patterson, as he
took hold of it in an undeveloped state and by
sinking to a proper depth, and providing the
necessary means and appliauces, has made it
an uubounded success. There is a 20-stamp
mill erected on the grottnd and every thing
bide fair for a large and steady yield of gold.
Mr. D. T. Hughes, the Superintendent, deserves great credit for the able and efficient
manner in which he bas opened this mine and
brought it, within the period of one year, from
obscurity to the position of one of the moat
promising mines in the state,