Enter a name, company, place or keywords to search across this item. Then click "Search" (or hit Enter).
Collection: Books and Periodicals > Mining & Scientific Press
Volume 28 (1874) (430 pages)
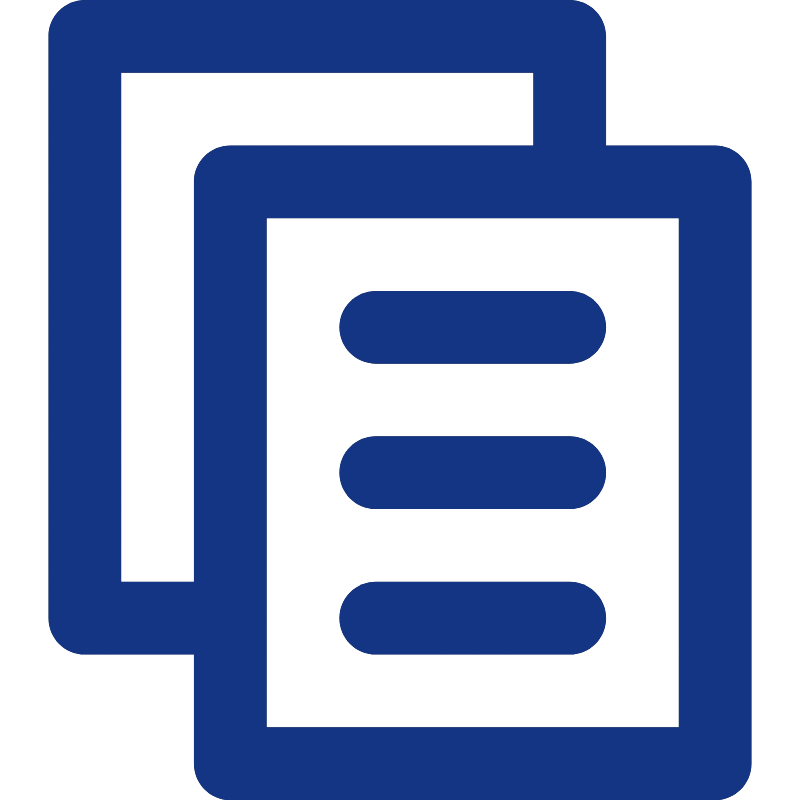
Copy the Page Text to the Clipboard
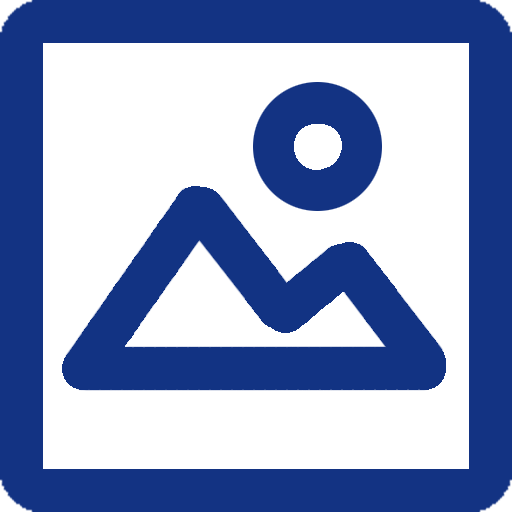
Show the Page Image
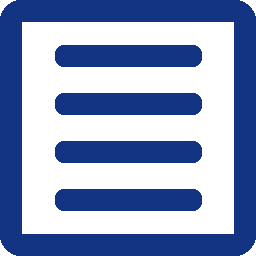
Show the Image Page Text
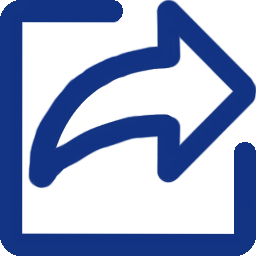
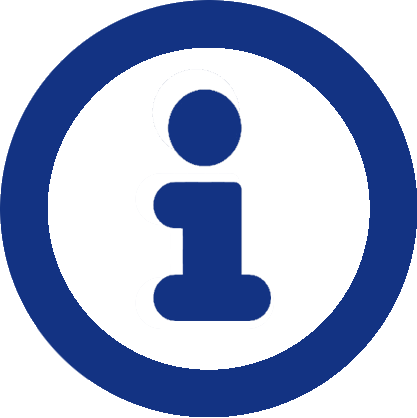
More Information About this Image
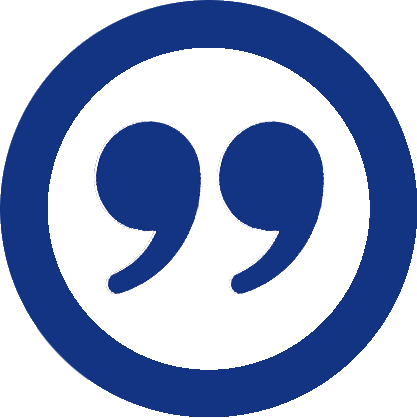
Get a Citation for Page or Image - Copy to the Clipboard
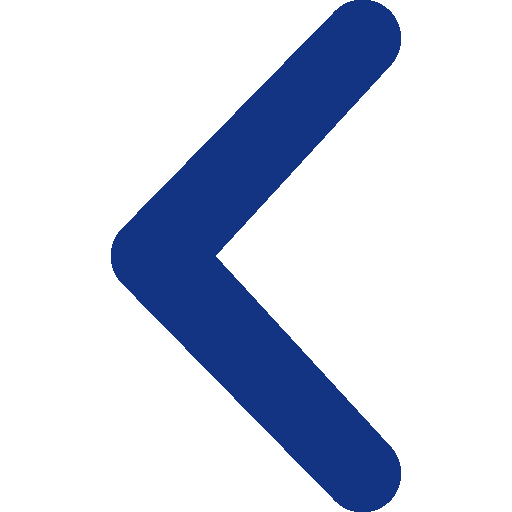
Go to the Previous Page (or Left Arrow key)
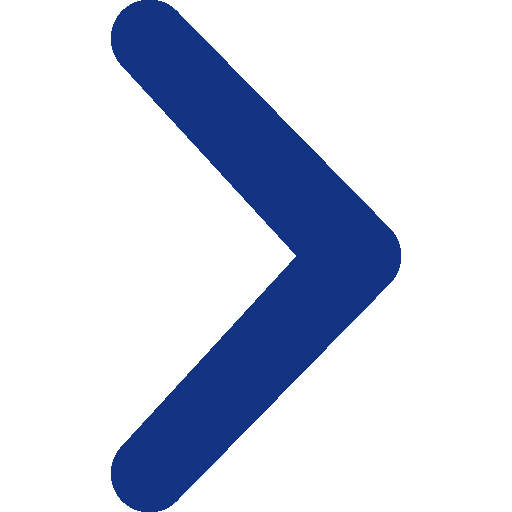
Go to the Next Page (or Right Arrow key)
Page: of 430
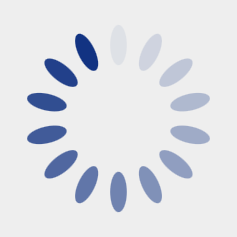
22 MINING AND SCIENTIFIC PRESS. (January 10, 1874.
The Chilian Method of Amalgamation.
Mr. Frederick Prime, Professor of Motallurgy in Lafayette College, Haston, Pennsylyania, has furnished from a French source tbe
following account of this process to the American Chemist:
Tbe first process employed in Cbili was/that
of the ordinary patio, but this was soon supplanted by another method which formed the
basis of that now in use, This consisted of
treating rich sulphurets in copper vessels witb
oupric sulphate, sodium chloride, and mercury.
At the end of a little time almost the whole of
the silver was amalgamated, heing, however,
only accomplished at the expense of a large
amonnt of mercury, the loss frequently being
200 to 250 per 100 of silver; in spite of which
this process was frequently employed for tbe
treatmeut of o1es coutaining more than 0:02
per cent. silver, owing hoth to tbe rapidity of
the operation, it taking less thau two hours
when aided by heat, as also to the small percentage of metal (searcely 0-0002 to 0.0003 per
cent.) left in the tailings. The enormous
amouuts of argentic chloride, iodide, and
chloro-hromide prodnced at Chanarcillo soon
demanded a more rapid, though less exact, process than the older one. In order to obtain
some idea of the amount of ore requiring
treatment, it will suffice to mention that the
single mine of Descuhridora produced in the
years 1831—51, the sum of ninety three millions
of dollars.
In the new process applied to these-ores,
they were crushed and nulverised as in the old
method. The pulverised ore was carried bya
stream of water to settling basins of sheet iron,
614 feet in diameter, and 934 feet deep. The
stream was conducted iu turn to different basins, which, when once filled, are left to stand
from eight to ten hours to permit the slimes
suspended in the water to settle at the bottom.
At the end of this period the clarified water
wae decanted off and the slimes were transferred to tinas. These tinas consist of wooden
yats, haying a cast iron bottom, and are 5 feet
10 inches by 3 feet 11 inches. These are provided in the line of their axes with a shaft hay‘ing cast iron arms which slide over the bottom
of the vat. The charge placed in these tinas
was aboutaton andahalf. The ores are a
mixture of chlorides, iodides and bromides,
haying a gangue composed of the carhonates
of lime and baryta as well as clay and oxide of
irou. The charge of tbe vat was completed by
the addition of mercury, about twenty times as
much of thisbeing added as there is silver in the
ore, Tbe shaft was then set in rotation, making
ahout fonr revolutions per minute. This opperation lasted twenty-fonr hours, at the end
of wbicb the amalgamation was supnosed to
be completed. A stream of water was then introduced, and the rotation continued. The
slimes were removed by the water, and carried
into settling basins. When the water ran
clear from the vats an orifice was opened in
the lower portion of the vat, and the mercury
aud amalgam which ran out were received in a
cast iron vessel, called cocha. The amalgam
was then sqneezed in athick piece of cotion,
and then laid aside for distillation.
Tbe wages, loss of mercury, arid various expenses cost $9 30 per ton for ores containing
less than 0.005 per cent. silver. The entire
operation, including crushing, took about sixteen hours. The tailings carried off by the
current of water, whicb were caught in settling
hasing, contained 0.0008 to 0.001 per cent. silver,
in the case of ores of the ahove mentioued
richness, and never exceeded 0.002 for richer
ores of the same character. The silver obtained contained scarcely 0.01 per cent. of impurities.
The process just described subsequently underwent several modifications. The time oocupied in treating the orein tbe vats, exclusive of lixiviation, was reduced to six hours;
and ores were treated in this manner containjug as high as 30 per cent. silver.
Owing to the increase in tbe proportion of
sulphurets as the mines were suuk deeper, the
results of the method of amalgamation just described nnderwent modifications; the percentage of metal in tbe tailings being angmented to
euch a degree as to diminish the yield of silver.
The tailinge, which were thrown to one side
at the time of amalgamation, formed near the
works enormoue masses of poor ores, whose
contente increased daily; the more so, as to
theee were added snch ores as were thrown
aside when picking over the ores.
Attempte were made to recover the silver
contained in these large bodiee of tailinge, for
whicb purpose various experiments were tried.
The first ouetried was the Freiherg process of
roaeting and chlorination; the results obtained
were very unsatisfactory, owing to the inexpetience of the workmen, Sixperiments were
then made by chlorination and subsequent
treatment with ammonia, which were still more
uneuceeseful, owing to the high price of ammonia. The argentic sulpbate process (Ziervogel’e) did not yield any more satisfactory
resulte,
Recourse was then had to the process wbicb
we have first described, and which had been so
long abandoued, As we have stated, rich ores
called negrillo, which were sulphurets, were
treated in copper kettlee together with cupric
sulphate, sodium cbloride and mercury. The
reactions which took place were the followiug:
The cupric eulphate was transformed iuto
protochloride in the presence of sodium chlotide, thus: CnSO;+2NaCl=CuCle+Naz,S0,.
‘Tbe heated cupric protochloride coming in contact with the copper of the kettle formed cubchloride—Cu2Cl+ Ou=Cu2Clo.° The cupric
subchloride, in the presence of argentic sulphide and mercury, reacted on the sulphide,
the affiuity of the mercury for silver p:omoting
tbe reaction—Ag2S+CuzCle +nHg=2AgHe+
CuCl, +CuS+(n-2)Hg. In tbis manner tbe
amalgam was formed.
As we have seen, this process, as formerly
carried on, occasioned the loss of a large amount
of mercury. The reaction by which the cupric
protoohloride was converted into suhchloride
was at that period at the expense of the copper
kettles and the mercury. Tbns @ great loss of
mercury was occasioned, and the copper vessels were rapidly destroyed. Wheu, therefore,
aretnrn was made to this process, the first
thing sought for was the production of the suhchloride in special vessels and by other means.
Recourse was bad to the following method:—
The sodium chlorideis dissolved in water; 5
parts of salt per 100 of ore. Cupric sulphate
is also dissolved in water nntila Baumé’s aerometer indicates 209. Sudium cbloride is added
to satnration. By this means the oupric sulpbate ‘is converted to protocbloride. ‘Tbe protochloride is then transferred to a wooden vat,
into which metallic copper is charged at tho
same time, The liquors in the vat are then
made to boil by introducing steam at a pressure
of three atmospheres. At a temperature of
100° CG, the enprie chloride reacts on the metallic copper, and thns forms tbe subchloride
which is subsequently employed iu tbe amalgamation. Tbe reaction is known to be finished when, on taking 50 c. o. of the solution,
and introducing it into a liter of water, the oxychloride precipitates as a white powder, leaving the liquid entirely colorless. The subchloride is used as soon as made, and care
must he taken to preserve it from contact with
the air so as to avoid the formation of insoluble oxychloride. To prevent this oxidation
the solution is slightly acidulated with sulphuric acid. We will now proceed to the treatmeut proper of tbe ores.
The ores are first crnshed. For tbis purpose
au apparatus called trapiche is employed, resembling the mill employed in the manufacture of oil. Two vertical cast-iron wheels, each
weighing about four tons, form the chief portion of the machine; each of these has a rim of
wrought iron or steel. These wheels are monnted on arms set in motion by a motor of some
kind. Tbey are given a velocity of ten to
twelve revolutions per miunte and rotate on a
disk, called solera, made either of cast iron or
steel, and.on which the ore to be pulverised is
spread. The ore is thus crusbed to a fine
powder. While the wheels are rotating a
current of water is made to flow contiuuously,
which carries off the ore as it is crushed. ‘The
quantity of water depends on the fiueness to
which the ore is to be crushed. ‘The current of
water is theu made to flow through a succession
of tanks, in which it deposits the ore it has
carried off. The water escapes perfectly clear
from tbe last reservoir. When the first tank
is completely filled with ore, the current water
is cut off, and the slimes allowed to precipitate
for eight hours. The clarified water is decanted and the slimes, forming athick paste, are
shovelled out on toa level floor, where they
are left until they are oompletely dried by the
air. The capacity of each tank is ahout
1614 feet by 6% feet at the base, and is 3 feet
4 inches high.
In the amalgamation proper the ore, properly dried, is charged into casks wbose capacity varies from one to four tons; those of four
tons capacity being preferred at present, whose
dimensions are 5 feet 10 inches by 4 feet 10%
iuches; the thickness of tbe staves is about 3
inebes. The arrangement of tbe casks is almost identical witb tbat formerly employed at
Freiberg.
A charge is composed of four tons of ore
witha sufficient amount of saumure to form a
tbick paste. A varyiug quantity of magistral
is added, depending on the richuess of the ore
and the natnre of the gangue. When the latter
is calcareous, more magisiral is used than when
itis argillaceous, or ferruginous, since the caleareous gangue decomposes a portion of the
cupric subchloride. For an ore containing less
tban 0.002 per cent. silver having a mixed
gangue, from 28 to 38 liters of magistralis used.
‘The casks are made to rotate for twenty to
thirty minutes, in order to give the paste time
to form; then the mercury is introduced, being
about twenty to twenty-five times the amount
of the silver inthe ore. The rotation of the
casks is then continned attbe rate of four or
five revolutious per minnte. Six hours suffice
to complete tbe operation.
If thé ores eubjected to this treatment contain
alarge proportion of argeutie chloride or bromide, 25 ibs. of lead are added to the mercury
for every 100 ibs. of silver. This lead is added
as amalgam; it eerves to prevent tne chloridation of the mercury, The reaction of the argentic chlorideis: 2AgCl+Cu2Cle +nHg=-2Cu
Clo+2AgHg+(n—2)Hg. The lead chloridieee
more readily than the merenry; tbe cblorine
and bromine set at liberty by the decomposition of the argentic chlorides and bromides reacting on the metal; thue avoiding, in the first
place, the loss of mereury which would result
from the cbemical combination; and, secondly,
another loss, much more cousiderahle and
purely mechanical, due to the division of the
mercury into little drope by the mercuric
chloride, which, when once formed, envelops
them in a thiu pellicle which destroys the homogeneity of tbe metal, and prevents it from
reuniting. The mercury is thus reduced toa
powder, occasioning great loss. The use of
ae reduces this losg from 150 to 25 parts per
100.
When the amalgamation is completed, the
next step is to wash the amalgam, which oneration is performed the same as in the Freiberg
process.
After which follows the refining of the amalgam,which contains cupric oxide and sulphide.
The first of these is formed by the reaction of
the lime of the gangue on the protochloride,
the last by the reaction of the magistral on the
argentic snlphide. The refining is divided into
two parts, the mechanical and the chemical.
Tbe former is peiformed in a tina analogous to
that already descrihed, the process beiug to
oharge the amalgam into the vat, adding ten
parts of mercury to 100 of the former. A current of water is then introduced, and the shaft
is made to rotate at the rate of sixty revolutions
per minute. Inthis manner the whole of the
cupric sulphide and a very small qnautity of
the oxide are removed. This operation is finished when tho water escapes perfectly clear.
To proceed to the chemical refining, the water
in the vat is permitted to escape, aud two parts
of ammonium carbonate per 100 amalgam are
added. The shaft is caused to rotate from four
to five honrs, and the amalgam is then washed,
when it is fouud to he entirely freed from cupric oxide. :
The distillation of the amalgam takes place
in a closed vessel per descensu. The furnace is
formed hy a cast iron hell, the lower portion of
which stands in a basin of water iu which the
mercury condenses. The upper portiou of the
bell is surrounded by a circular wall; the fuel
being charged into the anuular space between
tbe wall and tbe bsll, which is about 3 to5
inches.
The spongy silver (pina) which is obtained is
remelted in a reverberatory. It is necessary to
thoroughly rable the meiallic bath; the remnant of arsenic remaining 1s thus removed by
contact with the iron tools, forming au iron
arsenide which floats on the surface and iseasily removed. The silver thus obtained is 980
thousanths fine.
The process which has just bsen described
is applicable to all silver ores, with the exception of argentlferons copper pyrites, palena,
blende, and sucb ores as contain more than 1
per ceut. of free arsenic, the latter largely augmenting the loss of mercury.
In this manner it is possible to treat tailiugs
uot containing more than 0.0004 per cent., and
ores nof containing over 0.0006 per cent. silver.
So long as the richness of the ores subjected to
this treatment doos not exceed 0.005 per cent.,
the tailings obtained do not contain more than
0.00015 to 0.0002 per cent. silver.
The ores subjected to treatment are never
reduced to an equal percentage by mixing, as it
is found much more profitable to treat the rich
ores separately. In this case the operation is
completed much more rapidly, the interest on
the capital thus running for a much sborter
period, tbus compensating, toa great extent,
for the cost of treating tbe refuse of the operatiou.
Tbe mercury which has been used five or six
times hecomes so charged with impurities as to
retard the amalgamation. It is purified by
adding 20 grammes of sodium amalgam to
every 200 tbs. of mercury.
The works are nsually placed near a stream
of water, in order to have both the water and
motive power necessary for the various operations.
Works of sufficient capacity to treat eight
tons per day cousist of—1. An area of 550
yards for dumping ores. 2. Two trapicheset in
motion bya motor of six horse-power. 3. Four
basins. 4, An area of 1,100 yards for drying
the pulverized ores. 5. Two amalgamating
casks, with a motor of eigbt horse-power. 6.
Avat to receive the wasb-water of tbe casks
and to recover the comminuted meroury. 7.
A vat for washing the amalgam. 8. A distilling
fnrnace. 9. A melting furnace. 10. A wooden
vat for the preparation of the magistral with a
small caldron. 11. Two vats in which to dissolve the sulphate. 12. A basin constructed of
hydraulic cement for the saumure. 13. A caldron in which to treat tho saumure. To which
must be added the basins for clarifying and
purifying the waters.
These last are made to pass through quicklime in order to recover tbe copper salts. They
are thns rendered limpid and potable. The
persons employed consist of a superintendent,
an assistant superintendent, an assayer, a clerk,
a foremau, and ten workmen.
The cost per ton of ore, containing 0°002 per
cent. silver, is—pulverizing, 1°49 dols.; mercury,. magistral saumure, 3°72 dole.; refiniug tbe
amalgam, ‘04 dol.; distillation, -04 dol.; melting and refining, ‘09 dol.; tools and varioue expenses, ‘93 dol. to 1 dol. 0:03c. [These values
are giveu in coin. J
This does not include interest, the operation
takiug euch a sbort time, nor a sinking-fund of
the capital.
The great charm of the Cbilian method of
amalgamation isits great simplicity. This process eliminates a large number of the operations preceding the amalgamation, or considerably simplifies them. If, for example, it be
compared with the European method of amalgamation as formerly carried on at Freiberg,
it will be found to be infinitely superior both
for rapidity aud eimplicity. It eutirely does
away with the difficult operation of roasting,
which is delicate in its manipulation and the
cause of almost all the loss of silver. Even
when compared with the American method of
amalgamation as carried on iu Mexico, it is infinitely superior as regards rapidity. It replacesthe doubtful and hypothotical reactions
of thie process by chemical reactions which are
both exact and cloarly defined. In one word,
it solves in the most simple manner a question
in silver motallurgy wbicb has never been
hitherto accomplished but by roundabout
means, i. e., the elimination of the sulphur and
tbe direct nnion of the silver and meroury.
Finally it may be stated that, while elsewbere
amalgamation must give way to the fusiou witb
lead as soon as this hecomes possihle, as applied with us it will not he the case, sinco it
greatly surpasses this process. Itis unkuown
who was the inventor of this method; it can
only be stated that this process hae been constantly in use at Copiapo siuce 1862.
Divisibility of Quicksilver, Gold and
Silver.
The Virginia Enterprise says: ‘Tbe divisibility of quicksilver, and also of silver and
gold, as shown by the mining operations conducted in this State, is almost incompreheusibly great, and would scem to bo almost illimitahle, particularly in the case of the metal
first named, A globule of quicksilver may be
divided until uo longer visible to tbe naked
eye, and indeed scarcely visible under a powerful microscope, yet even the most minute
subdivisions shall be fonnd to contain silver or
gold, perhaps both. How infinitesimally
small, then, must be the particles of silver or
gold contaiued in one of tbese iuvisible and
immeasurable globules of mercury! In regard
to the astonishing divisibility of the metal
mentioned, we bave just learned some interesting facts of Dr. Buncher, Superintendent of
the Rock Point Mill, Daytou. This gentleman informs us, that some time since, when
working in his mill for a considerable period,
an ore in which gold largely predominated, he
used every precantion to guard against loss.
In additiou to the usual settling tanks, he
eaused to be dug in the grouud a numher of
large pits, into which the waste water flowed
after leaving the tanks. After loaving these
pits, the water passed off in a small flume, and
to the eye appeared as clear as tbe water of
the purest monntain stream. For the sake of
experiment, Mr. Buncber ooated a copper
bowl with quicksilver, and placedit in such a
position that tbe wator of the flume shonld fall
into it. He also placed in the flume, below
the bowl, some copper riffles, properly coated
with quicksilver. Altbough the water passing
through tbe flume seemed to be perfectly
clear, yet at tbe end of three months the bowl
and rifflss were cleaned up and over $100
worth of amalgam ohtained. His mill is driven
by water from Carson River, and carried for a
considerahle distance through a large wooden
flume. A month or two since it became necessary to shut off the water and repair a portion
of tbis flume. In making the necessary repairs it was found that in many places tbe
heads of the nails driven into its bottom had
been thickly coated with amalgam. Witbin
the distance of about three rods aloug the bottom of the flume the workmen engaged in
making the flumo collected over an ounco of
amalgam. This was where there were no copper plates or other special facilities for catebing
the floating particles of quicksilver. The
water flowing through tbe flume was taken
from the river below a number of large mills,
and, tbough far from heing clear, would never
have been suspected of contuining floating
quicksilver in such quautities as to amalgamate the heads of iron nails. In order to amalgamate iron it must bescratched or polisbed
while immersed in quicksilver, tberefore, it
will be seen that much material must have
passed by before the occurrence of tbe accideuts required for the commencement of the
aocumnlations found on tbe nails. As anotber
evidence that qnicksilver in sousiderable qnantities floats iu the water of flumes and streams
below reductiou works in a state of invisible
divisiou, and yet carries with it the precious
metals, Dr. Buneber gave us this additional
evidence: On a certain occasion one of his
workmen required a piece ofcopper. Remembering to have eeen some old sbeets of tbat
metal lying near the waste gate of the main
flume, he went to the spot, and hauled them
out of « puddle in wbich they were lying, and
found tbem beavily coated with amalgam, and
so eateu up that they were hardly thicker thau
writing paper. The water pouring out througb
the waste-gate had a fall of about fifteen feet.
It did not fall directly upon the oopper plates,
but in sucb a manner 2s to keep them constantly splashed and wet. Mr. Buncher thinks
the plates had lain in the place four or five
years. Over a pound of amalgam was scraped
off them. It appears to us that in these soveral etriking instancee of the treacherous and
unspecting floating away of the precious metals there is for mill-men food for reflection,
and for inventors a field in which to reap hoth
profit and distinction.”
Countrerreirino Trap— Marks. — Reporte
have been received at the Treasury Department from Mr. Denman, Special Agent at
Shaughae, stating that he expected to bein
Calcutta on the 10th of January. He investigated the cause of the decrease on American
exportation of drills to China, and ascertained
that it was caused by British drills, the mannfactnrere of which imitated American trademarks and undersell American goods. The
Chinese prefer American drills, butthe fraudulent trade-marks on British goods have deceived
purchasers. Our exportation has fallen off from
250,000 to 40,000 pieces per annum, while the
British exportatious increased from 14,000 to
250,000 picces.