Enter a name, company, place or keywords to search across this item. Then click "Search" (or hit Enter).
Collection: Books and Periodicals > Mining & Scientific Press
Volume 39 (1879) (446 pages)
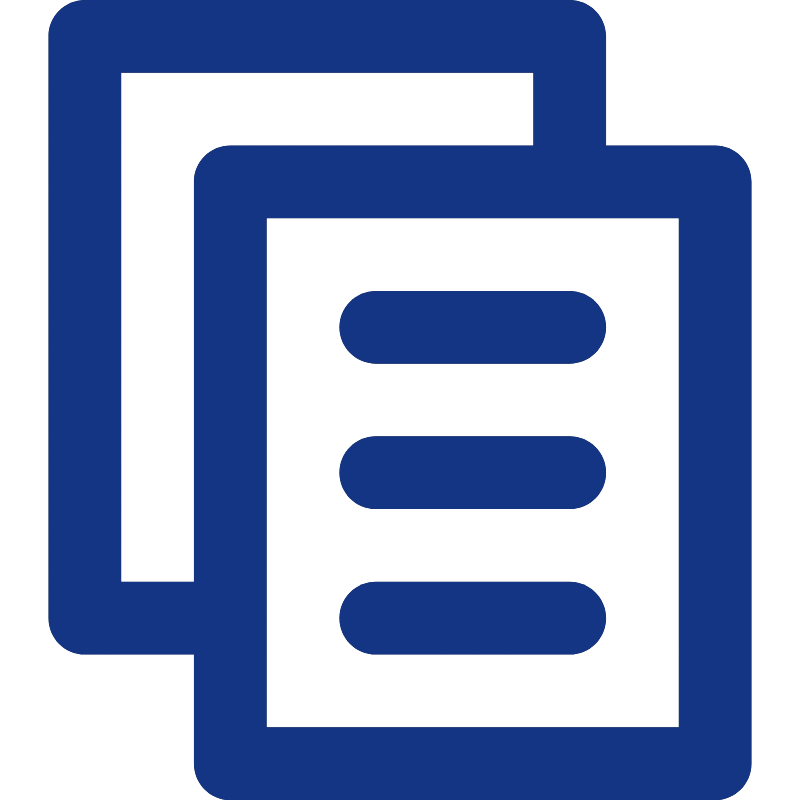
Copy the Page Text to the Clipboard
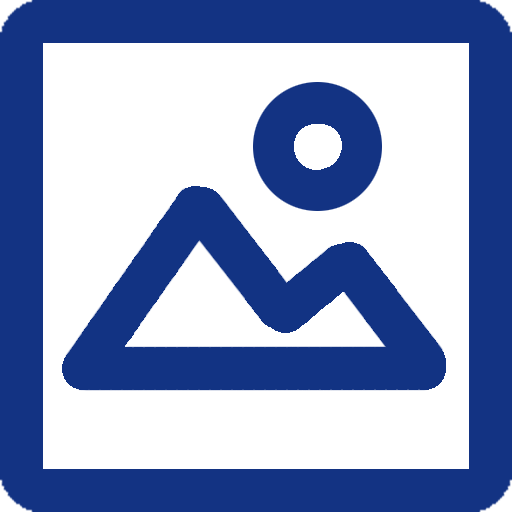
Show the Page Image
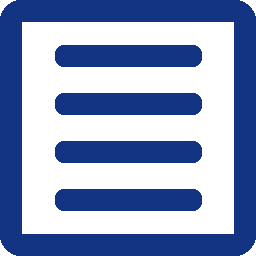
Show the Image Page Text
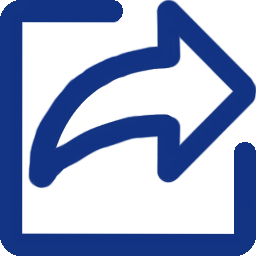
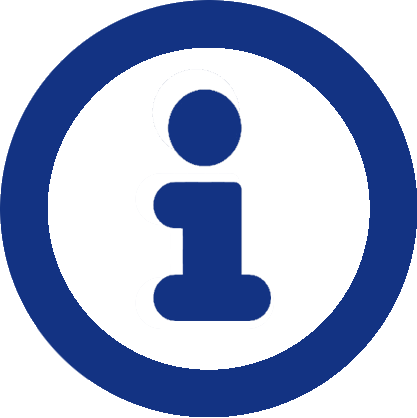
More Information About this Image
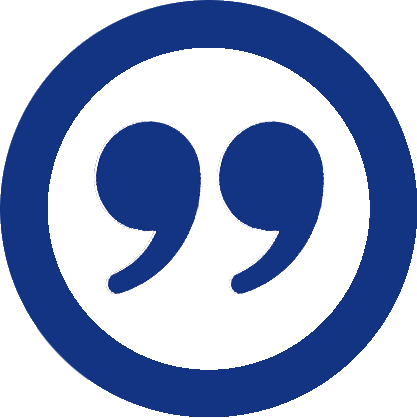
Get a Citation for Page or Image - Copy to the Clipboard
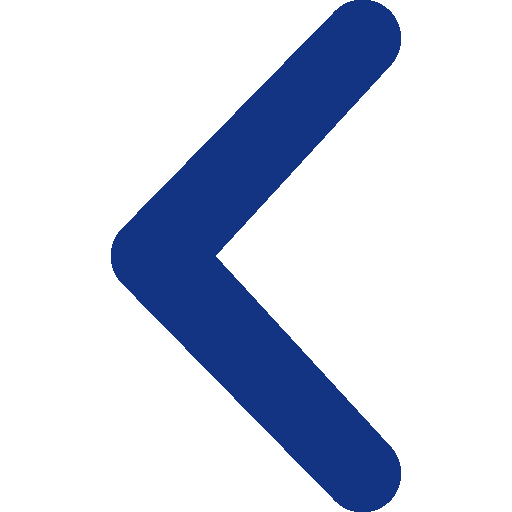
Go to the Previous Page (or Left Arrow key)
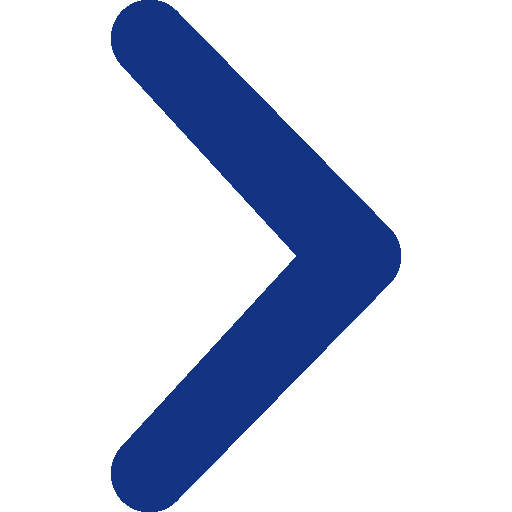
Go to the Next Page (or Right Arrow key)
Page: of 446
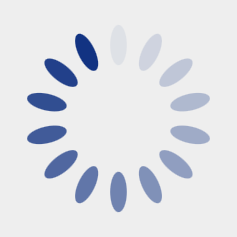
MINING AND SCIENTIFIC PRESS.
[July 5, 1879.
5
{GorresPonDeENce.
of corrospondents.—Eps We admit, dorsed, opini
Shasta County.
Epirors Press:—At Mad Ox, seven miles
above Whisky Town, we find the quartz mill
owned by Messrs. Grotafend, Brickford & Co.,
in fine running order, with its double turbine
water wheel, from A. Myers, San Francisco.
The mill is running day and night, the partics
are confident of a good thing in their mine,
which is well located with a large body of finelooking quartz now in sight. The extension of
tbis mine known as the Peckham mine, now
owned by A, Saulan, Warfield, Scott & Co., is
turning out a large amount of good quartz,
worked by an arastra, pays from $100 to $140 per
ton, ledge from 3 to 54 feet in thickness.
On Mad Mule
Mr. Banghart is working his seam diggings
very quietly, but with satisfactory results.
Since 1866 he has bis new tunnel in 500 feet,
and is within a few feet of his pay chimuey, or
seam, which is very rich. Ex-Sheriff Jackson
is working the extension with good prospects.
The diggings have heen very rich in the gulches
in tbis vicinity in past years. , :
The Bell & Knox mine on Grizzly gulch, in
same district, bas yielded a large amount of
gold during the past two years.
The mining interests around French Gulch
are very encouraging. Messrs. John, Souter,
Simes & Co. are getting the old Washington
mill and mine in running order again, as they
have found new bodies of ore. The quartz in
this district is gold bearing. F. McConnell and
H. Dorr have a fine prospect higher up the
mountain, their ledge is hetween slate and
porphyry, rock averaging from $40 to $70 per
ton, worked by an arastraright at tbe mine. V.
Kern is also running an arastra on tbe north
fork of the creek with equally good results.
Passing over the mountain at an altitude of
4,100 feet (into Trinity county), we find Deadwood gulch, on which five arastras are now
running—George Keine, two; G. F. Deiner, two;
Waver Sehastian, one. Mr. Willey and Mr.
Davis are also working very rich ore from their
mines. Ores in this district run from $70 to
$120 per ton, and some has run even higber
than that. There is no doubt but this will
prove a fine district, it is well located, formation
elate and porphyry, the same as French Gulch
district, and the gold of good quality. B.
Chrome Mines in San Luis Obispo.
Epirors Press:—On the afternoon of Saturday last I had tbe pleasure of visiting with an
acquaintance the ‘‘chrome” mines among the
hills about eight miles distant. For about five
miles the road leads through a picturesque valley, watered by a perennial stream which is
fringed with a rich growth of grass and sycamore trees. In passing through we noticed evidences that more than one picnic party bad
practically appreciated the inviting ebade. On
leaving this valley we ascended the ‘‘grade,”
which is a road cut along the side of the mountain eomewhat spirally, and is of just sufficient
width for one team only; though there are ‘‘bays”
here and tbere for tbe convenience of teams
passing one anotber. Where the “grade” was
steepest and narrowest, and in every uncomfortable way most suggestive, tbe hill bore nothing to which in an emergency one could cling
but wild oats; above this there was a tbick
chaparral growtb interpersed with pines and
cedars; here too were some large manzanita
busbes whose stems were 10 or 11 inches in diameter, Having attained tbe bighest point,
and seen four Chinamen just beginning a new
miue, we returned, and ou the way halted for
water at the house of Mr. Louis G, Flores, of
San Luis Obispo, who owns the mines and a
large area ofland. We were fortunate enough
to fiud him at home, and he at once offered us
his hospitalities. Having refresbed ourselves
and tbe horses, Mr. Wlores conducted us _ to his
most productive mine, Here we found men at
work in a tunnel running abont 200 feet into a
hill. Mr. Flores described to us tbe cbaracteristica of the chrome ore, and pointed out the
dips and leads of tbe various veins, and sbowed
ns one vein that bad increased in breadth as the
minere followed it, until it developed into a
huge eubterraneous mound of pure cbrome,
The ore ie eorted, screened, and then hauled to
the depot of the S. L. O. andS. M. V. RB. R.,
whence it is taken hy rail to Port Harford,
thence to Baltimore by way of Sau Francisco,
The only factory in the country, for using thie
chrome ore at present, is at Baltimore. The
price paid at the depot here ie $8 per ton, which,
in the opinion of those qualified to judge, is not
a sufficient compeneation, We returned home
after an enjoyahle trip.
San Luie Obiepo, Cal., June 16th.
Great Western Quicksilver Mine.
Eprrors Press:—Among the first, if not the
first mine now being worked for mercury, is the
Great Western, near Middletown, in Lake
county, which bas for several years heen under
able management of the experienced mining
engineer, Andrew Rocca, now running a force
of 250 men, Tbe mine discharges the ores hy
tunnel and trains of borse cars rigbt at the
furnaces and assorting sheds, Tbe tunnel for
main discharge is now in a distance of half a
mile, There is also a tunnel discharging
througb the mountain on the west side to
anotber furnace there. The principal extracting of quicksilver is done hy one fine-ore furnace ef the capacity of 13 tons in 24 hours; and
three coarse-ore furnaces, each of capacity of 35
tons in 24 hours. Of the coarse-ore furnaces,
two are Greene’s excellent furnaces; one of
Coult’s—patented in 1867 by Josepb Coult, then
of Pope Valley, but now in Texas. This furnace gives the best, easiest and cheapest results;
does not cost one-fourth as mucb as tbe others
—$5,000 will put up two of them witb condensers. The ine-ore condenser uses,a Livermore
condenser. Uses Hercules Giant powder as the
best and safest—have tested all kinds—using
ahout $600 worth per montb; average about 160
shots or blasts each six hours.
Mr, Rocca is a progressive man and has introduced many new, original and practical ideas in
his various machines. His glass-roofed condensers are proving a perfect success. The flow
of metal from tbe furnaces has not ceased for
the last three years, yielding 500 to 600 flasks
per month, or about 7,000 to 8,000 flasks per
annum, which is sent hy freight teams to Cal.
istoga depot at $6 per ton over Lawley’s toll
road. Men work 10-hour shifte between 7 a.
mu. and 6 p, m., and from 7 P. um. to 6 A. M.
The Sulphur Bank and Oat Hill mines are doing well, hut not working up to full capacity.
The latter mine is considered an excellent mine
and under very successful management.
Dr. Baker, below the lake six miles, is doing
well for the amount of capital now at hie command, He claims some successful improvements in furnace and condensers, and deserves
ample success for his great perseverance where
capital was lacking. B. W. C.
Middletown, June 9th.
The Telluride Ores of Gold.—No. 4.
(Thesis by Russeun L. Dunn, College of Mines, University
of California.]
Special Processes.
Smelting with copper oree usually more or
less auriferous and argentiferous to a copper
matte. Tbie is the process employed at the
Boston and Colorado works at present. When
first introduced the Ziervogel process was used
to part the gold and silver from tbe copper ;
this, it is said on account of the expensiveness
of the chemicals employed, was abandoned.
Since then a secret metbod, invented by Prof
Pearce, bas been used, and is claimed to give
better and cheaper results than any other yet
applied, Tbe Boston and Colorado works have
treated the greater portion of tbe telluride ores
of Colorado.
Smelting with auriferous iron pyrites to an
iron matte. Tbie process, so far as I bave information, has never been used with telluride
ores, though recommended,
Smelting witb lead ores to base bullion is
often used and eeems to be fairly successful.
Very rich ores are not usually treated by this
method. Tbe process is in use in Boyd’s smelting works ‘at Boulder City, Colorado, on oree
too poor in gold and silver to be smelted in a
lead hath. The base bullion can be refined and
parted by the usual methods. As compared
with the Copper Matte process described ahove,
it is said not to give as high a percentage of return.
Smelting in a lead bath. Into a test of
melted lead very finely pulverized ore is fed in
quantities of from 10 Ibs. to 15 lbs. at a time.
The slag is skimmed off from time to time as it
accumulates in excess ; as soon as the lead is
sufficiently enriched it is removed and a fresh
charge of lead introduced, The relning and
parting of the enriched lead are done in the
usual way. Tbe same lead can be used over
and over again, the unrecoverable loss being
small, This process isin use in Boyd’s works
at Boulder city, Colorado.
_ Mr, Boyd has patented what he considers an
improvement hy which the ore as it ie fed into
the test is forced beneath the surface of the
melted lead and retained there until the tellurium minerals are decomposed and the tellurium
driven off. ‘Theoretically the principle seems
good, how it works practically Iam unable to
say as accounts vary,
Rich oree are sometimes smelted in cruciblee
with litharge and reduciug fluxes. A high per.
centage of metal is of course returned, but at a
proportionately bigher expenditure,
All of the crucible, and the cupellation lead
bath procese are quite costly, and with the exception of tbe latter only euitable ae experimental processee on a small ecale. None of
them, except under favorable circumetances,
can treat other than high gradee of ore.
The matte processee are tbe beet on a large
ecale. For them and for furnace pro in
too fine. At tbe Boston and Colorado works at
Denver, the ore ie crusbed by steel rolls so as to
pass through sieves of 10 holes to the running
inch. For cupel and crucible processes tbe ore
must be finely pnlverized. Tbe table will show
where smelting is and can be applied,
Amalgamation.
Very little need be said about tbie branch of
the metallurgy, as telluride ores will not amalgamate. Amalgamation ie decidedly the best
treatment for gold ores where it can be applied
directly to metallic gold in a finely divided condition, No other metbod will yield so high a
percentage of the gold in tbe ore at so lowa
cost. But mercury will not decompose tellurides so as to amalgamate tbe gold and silver in
tbem. Iam informed tbat the mercury cuts up
and blackens, acting very much as with base
metal cblorides and sulphates. In attempting
to mill some extremely rich ore from the Stanislaus mine in California, it was found tbat only
from 5% to 10% of the gold was saved; attempts
since made in Colorado bave succeeded no better.
Where there is much free gold and few tellurets and sulpburets in the rock, it is possihle
to crush tbe ore wet, run it through the amalgamation plent, and thence to concentrators
which will save tbe tellurets and sulpburets
and concentrate tbem to second class ore. I
know of no inetance in which tbis process is
employed at the present time, and frora general
principles it is only to bo recommeuded in the case
i above, where it is obviously more economical,
Roaeting.
The roasting of telluride ores is the most interesting as well as the moet important point in
connection with their metallurgy. It is true
that roasting is now practically abandoned on
account of the large loss of metal by volatilization, but if some economical mode were discovered by which the ore could be perfectly roasted
without loss, it would become used to the almost
entire exclusion of smelting. Roasting is the
only economical way of preparing mineralized
gold ores for amalgamation, All kinds of fur.
naces have been tried on these ores, reverberatory, Bruckner’s cylinders, and in fact almost
every roasting device which tbe ingenuity of
the metallurgist could invent,’and thue far,
none of them, judging from the length of time
they were used, are more than partially euccessful at the best.
The principal reason why roasting has not
been successful ie the volatility of gold, and in
a less degree silver, with tellurium and tellurous acid, Mr. Kustel, who in 1865 said that
the ores could be roasted in a reverberatory furnace euccessfully, made eome experiments on
ores from Colorado a few yearsago. He roasted
them himself in tbe sulphuret roasting furnace
connected with the cblorination plant at Grass
Valley, paying the most careful attention to the
rate of roasting and the regulation of the draft,
and the best result he was able to obtain showed
a loss by volatilization of 97%.
This peculiar volatilization of gold is one of the
unsolved problems of chemistry. It is said to
occur in roasting sulphurets, but some careful
experimente by Mr. Kustel convinced him that
in tbis case the loss was mecbanical and caused
by a too rapid roasting. Arsenic and antimony
seem to have more or less of the same power
(doubtful) of causing gold to vaporize. It is,
bowever, most marked with tellurium. Whetber
the gold vaporizes as gold or volatilizes as a
telluride of gold has not yet been discovered,
but the latter eupposition would seem to be the
most probable, although it may be both. Gold
is slightly volatile at high temperatures. A
rather curious instance of this property occurred
in the Boston and Colorado works at Black
Hawk, Colorado, eeveral yeare ago. In breaking up a hearth from a reverberatory furnace used
for roasting iron matte, flakes and wires of pure
bright gold were found in the quartz bed at some
distance below the eurface ofthe same. How
the gold got there from ahove is a mystery even
under the supposition (most probable) of vaporization and condensation.
It is necessary that telluride ores should be
crushed dry and very fine for thorough roasting. The usual plant for roasting and the
method of carrying on the process are the same
as are used for roasting ordinary auriferone iron
pyrites, only considerahle more attention must
be given to the manipulation, as the roasting
is much more delicate. As the ordinary roasting furnace is well known, it is not necessary
for me to give any description of it.
Willard’e furnace is peculiar both in construction and manner of working. Heat is
applied to the exterior by a fire underneath,
and the roasting goes on inside supported by
sawdust or some other finely divided oarbonaceoue matter which is mixed with the ore, A
hlast is used to supply air to tbe inside of tbe
furnace. The roasted ore can be treated in
three ways, viz., dry amalgamation, wet amalgamation and chlorination. By tbe lirst more
or less gold and floured amalgam are unavoidably lost, The fineness of division of tbe gold
and eilver ie eo extreme that the particles are
liahle to remain euspended in water and pass off
with the elimes in wet amalgamation. By
chlorination the silver ie of course loet unlees
anotber process be subsequently employed to
save it,
Roasting proceeses as a rule can treat equally
well all gradee of ore, hut tbe richer the ore
the more careful ehould be the manipulation,
Chemical Proceeses, Etc.
Under tbie head I include all of the eo-called
general tbe telluride ores sbould not be crushed
wet pro which bave or can be applied in
reducing telluride ores, I can learn of no in“to it by steel springs.
etance in which any of tbem bave been applied
on alarge scale as practical processes. Acids
bave been used to dissolve out tbe tellurium,
after which it was easy to extract the metal.
Such processes are, bowever, far too costly for
any but the ricbest ore.
Mr. Stewart made some experiments, or
rather teets, with bis modification of the Hunt
and Douglas copper reduction process, at
Georgetown, Col. Tbey were on a small scale,
hut he claims euccessful. His process will treat
ore of any grade without previous roasting,
Concentration.
It is found unprofitable to work low grades of
tbese ores by smelting raw, and it is therefore
necessary to concentrate first. By concentrating it hae been made possible to reduce all rock
coming from the mine with as low a value as
$15 or $20 per ton.
Tbe thorough concentration of telluride ores
ie somewhat difficult. Owing to the complete
dissemination of the small particles of mineral
the ore must be crushed very fine, and then of
course more or less will be lost in tbe tailings
and slimes from the macbines. Also in crushing fine, tbe brittle mineral is powdered, while
the gangue remaine in comparatively large particles—that is, the gangue and mineral are not
crusbed equally, thusmaking a preliminary sizing
of tbe crushed ore necessary, with the use of the
usual machines. It can be readily seen tbat the
German metbods, sieving and jigging, are not
applicable to sucb fine ore. The ordinary
modes of concentration employed in California
and on tbe Pacific coast for eulphurete are
mucb better. Buddles, cradles and blankethoxes all do good work, though by no means as
perfect as can be desired. A machine has been
in use in the last few years in the Telluride dietrict of Colorado, which seems to do better
work than any of the others. It is called tbe
Frue Vanning machine or ore concentrator. It
consists of an endless rubber belt moving upward by tbe revolving of the rollers on which it
is stretched, A rapid lateral vibration is given
Tbe ore and water are
fed continuously on the surface, and the tailings
discharged at the foot, while the concentratione
are wasbed off in a box filled with water,
tbrough which the belt travels. The macbine
ie perfectly automatic in action, hand labor only
being required from time to time to remove tbe
concentrations,
As regarde the absolute efficiency of these
machines (i. ¢., the percentage of the mineral in
a given grade of ore they will eave), accounts .
differ, The last described would seem to be tke
best, as the otbers bave been discarded almost
entirely for it. Even it, however, would not
seem to be all tbat is desired, from the fact that
it will not treat economically as low grades oftellurides as of other gold ores.
Very little more remains to be said of the .
beneficiation, except to note that there is still .
room for improvement.*: It bas been noticed by .
smeltere tbat certain fluxes, more particularly ;
limestone, seem to reduce the volatilization of f
the metal, and it is possible that some substance .
may yet be found which will bave the same in.
fluence in the roasting furnace. In wet pro.
cesses we may find tbe true metbod of working ;
these ores, but roasting, with amalgamation or .
chlorination are at present the most available ;
for improvement.
[Concluded ]
The Treatment of Auriferous and Ar
gentiferous Pyrites.
Tbe trouble experienced in dealing with #
sulphurets” is so well known that it will be .
unnecessary to say that every new method!
which will serve to reduce the cost and tbelosses of extracting gold, silver and copper from
ores running high in pyrites, deserves attention,
A recent modification of known methods ie that !
proposed by Mr, W, A. Dixon, who has made a:
series of experiments to test its value, so far as!
laboratory work can accomplish that object, He:
roasts the ore on a matte smelted from tbe ore:
in a muffle roasting furnace, and utilizes tbe
eulpburous acid formed for the manufacture of a
dilute sulphuric acid, in suitable combination :
chambere and condensation towere. Any
arsenious acid formed is deposited in a flue previous to the gases entering the combination
chamber, So far the process does notin anys .
way differ from existing methods. Before beihg,
discharged from the muffle furnace the roasted . I
ore is mixed with a proper amount of coal dust
or any other carhonaceous matter, and then it
is transferred to a reverberatory fnrnace, in
which a reducing flame is maintained. Thie
reduces the oxides, formed in the preliminary]
roasting, to metals. The material is then car.
ried into vats, where a large portion of the iron) M
ie extracted by means of the acid solution from
the towers in tbe shape of asulpbate. The re.
sidue, which contains free gold and silver, ig
amalgamated, If copper is preeent in coneiderable quantities, the process is somewhat modi.
fied. The ore, after baving been roasted in the
muffle furnace, ie lixiviated with an acid eolu. fs
tion of copper, and then with water. Tbe re.
sidue ie mixed with carhon and treated further
in the manner deecribed. Tbe procese ir
claimed to poseees the advantage of suffering
less from poor roasting and of being conducted
at a low temperature, witb ite attendant de. Kini
creaee of coet of fuel, of plant and of lose by ty
volatilization, There ie none of the expense
conneoted witb chlorinizing roasting nor any}
outlay for precipitants,—Jron Age. Bh