Enter a name, company, place or keywords to search across this item. Then click "Search" (or hit Enter).
Volume 048-4 - October 1994 (8 pages)
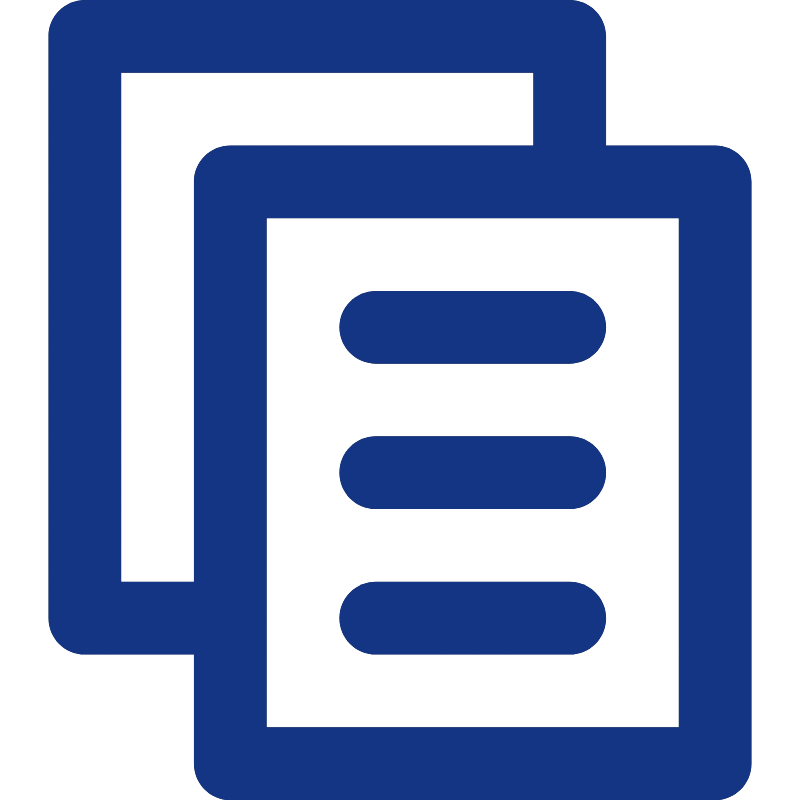
Copy the Page Text to the Clipboard
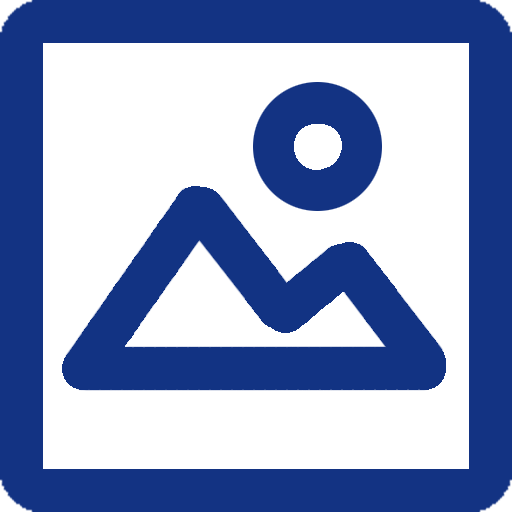
Show the Page Image
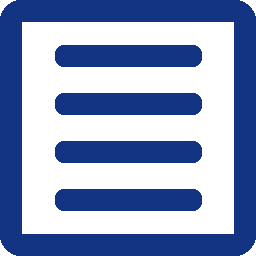
Show the Image Page Text
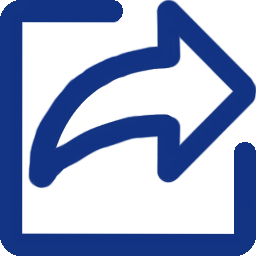
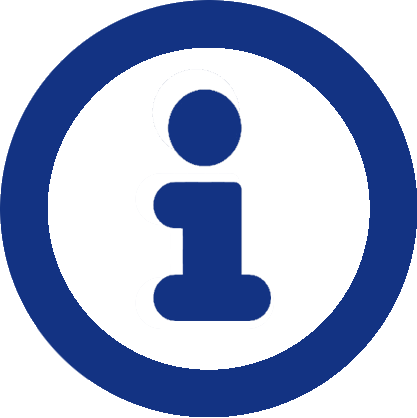
More Information About this Image
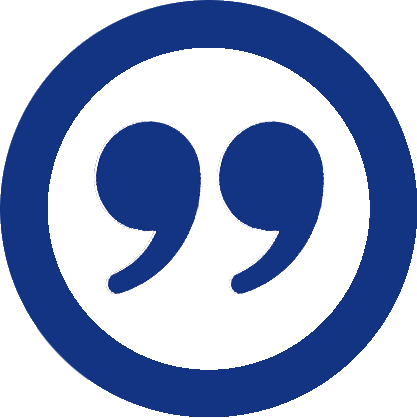
Get a Citation for Page or Image - Copy to the Clipboard
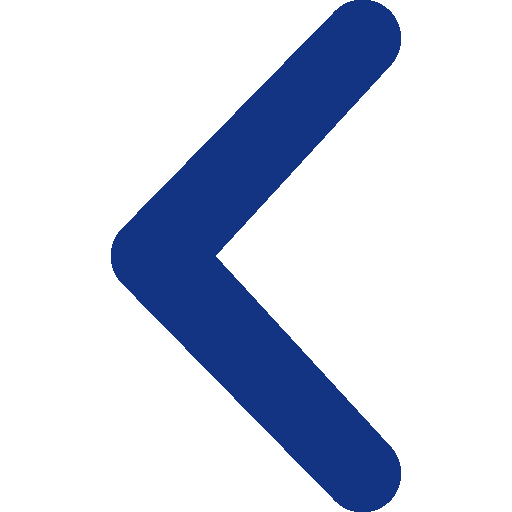
Go to the Previous Page (or Left Arrow key)
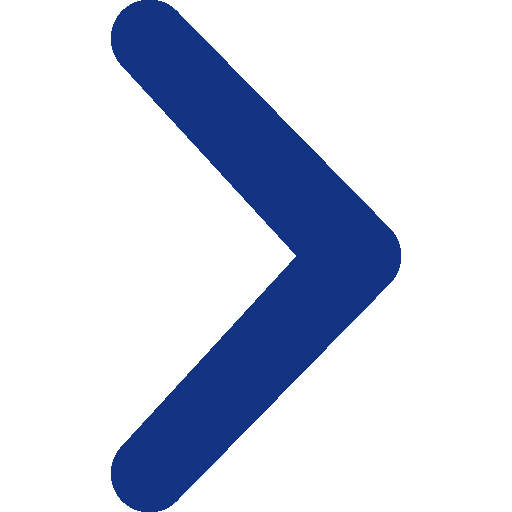
Go to the Next Page (or Right Arrow key)
Page: of 8
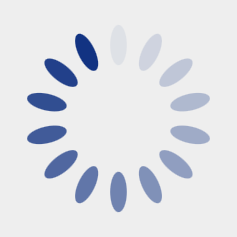
smith shop and a machine shop. This was true at the Miners’
Foundry. The difference in mode of operation of the three
parts of the expanded foundry can be looked upon as the
difference in the temperature at which the work was done:
¢ Inthe foundry proper, the iron was molten, so you poured
it into molds of the desired shape.
¢ Inthe blacksmith shop the iron was orange-hot and soft,
so you pounded it into shape.
¢ In the machine shop the iron was cold, so you cut it,
drilled it and ground it.
Tue MINERS’ FOUNDRY BEGAN OPERATIONS IN 1859
to provide cast iron machinery parts primarily for the mining
and timber industries. The main building was constructed of
rock because of the risk of fire—the scourge of the early
mining towns. According to several accounts, many of the
fires were not due to faulty stoves or carelessness, but to
arson—fires were set to damage or destroy buildings in order
to facilitate looting. This view is supported by the number of
fires that occurred during the summer season.
The Miners’ Foundry is located at 325 Spring Street, in
Nevada City, on the downhill side of the street. The principal
room is the large so-called Stone Hall, with the beautiful
chandeliers from a church in Brighton, England, and the
fireplace at one end. This Hall was the machine shop.
A narrow portion of the building, extending uphill, now
houses the studios of KVMR, the community radio station. It
amused to house the foundry offices.
The present foyer was the blacksmith shop. Adjacent to
that, to the east, are two rooms, or one room with a lightweight divider. This area was the foundry proper—in which
the two cupolas were located and where the molds were
poured. The largest castings were poured right on the floor.
Or rather, in it. The floor was sand, and the giant patterns
were carefully placed there, and the sand then packed all
around. It could require a week to prepare such a mold, for
example, the mold for a 16 foot diameter Pelton wheel.
The Great Hall, the large room at the lower level, now the
theater, is of corrugated metal construction rather than stone.
It was added at the time of World War II. It was used for steel
fabrication in the later years.
Products
Looking back at the early years, what did the foundry make?
Well, it made just about anything you might want made of
cast iron or sheet iron.
It made the huge stamp mills for the mines. The North
Star Powerhouse Museum has two fine examples. We have
the iron parts for one at the Miners’ Foundry now, waiting to
be reassembled. Making replacement shoes and dies, the
y@™ principal wearing parts, for these machines was a substantial
fraction of the foundry’s business. The foundry also made
mine cars, pulley wheels large and small, the famous Pelton
water wheels, which were a trademark of the foundry, and a
host of other items for the mining and lumber industries.
Later on, the foundry even made horse hitching posts—look
along Spring Street in front of the Odd Fellows Hall—
candlesticks, and yes, even prosaic manhole covers. It is
reported that near the end of its time, the foundry possessed
some 30,000 wooden patterns, so at one time or another, that
many different products were made.
Owners
We’ ve spoken enough about the technical side of things, let’s
now talk about people. There were three owners of the
foundry who were particularly noteworthy, each for different
reasons.
George Allan owned the foundry in the very early years,
from 1867 to 1907—-some 40 years. He was noteworthy for
being the owner when Lester Pelton, then 49 years of age,
came down from Camptonville in 1879 with a wooden model
of his strange-looking water wheel, to ask if the foundry
would consider manufacturing it. Mr. Allan would, and did.
The two men worked together extensively to develop a practical design for commercial manufacture. Since neither man
had any formal technical training, they did the work as
Edison, a contemporary of theirs, did his, by thinking and
experimentation. It is interesting to note in passing that Edison and Pelton were born in towns only thirty miles apart in
Ohio, and that Edison’s electric light and the Pelton water
wheel were both perfected for commercial manufacture in the
same year, 1879.
The first all-iron Pelton wheel, that is, a finished design
that could be offered for sale, was put to work in the Miners’
Foundry to drive the machine shop equipment. It also served
to demonstrate to potential customers the capability of the
water wheel, since it was only 24 inches in diameter, yet
drove all the machinery in the shop. This Pelton wheel still
exists. It is on display at the North Star Mine Powerhouse
Museum, in Grass Valley.
It is not surprising that George Allan was willing to take
on the development job with Lester Pelton. Allan himself was
an independent, self-reliant type like Pelton. Allan had left
his home in England at the age of 16, and traveling alone,
made his way to Canada. There he managed to find a variety
of jobs, some in outdoor construction work, some in offices
doing clerical work. At one point, he and two friends built a
small steam driven tugboat and managed to secure Canadian
goverment contracts to deliver supplies on Lake Ontario.
Years later, at the urging of a brother already living in
California, he came down to the United States and out to
California, where he went to work in gold mining. He eventually ended up buying the Miners’ Foundry from the original
owners, Messrs. Thom and Williams, after it had been in
business eight years. Allan knew nothing of the foundry trade
prior to his coming to America; he learned it all by experience in the mining country.
The second noteworthy owner, William Martin, bought the
31